Exploring Plastic Molding Electrical: Innovations in the Metal Fabrication Industry
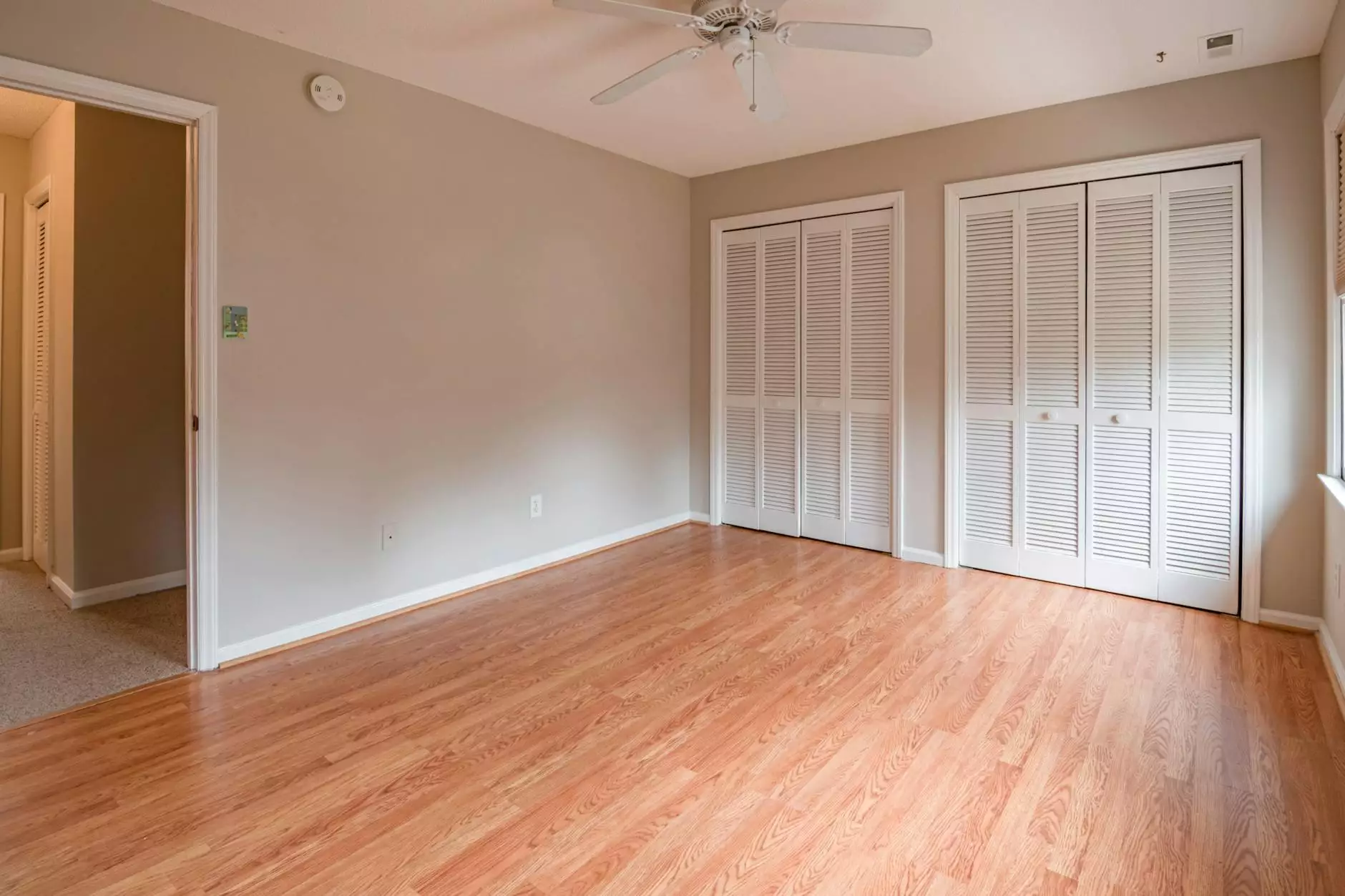
The realm of plastic molding electrical is making significant strides in the world of manufacturing. As businesses seek to innovate and improve product quality, they are embracing advanced technologies that enhance efficiency and reduce costs. Understanding the pivotal role that plastic molding plays, especially in the context of electrical applications, is essential for manufacturers aiming to stay competitive in today’s fast-paced market.
What is Plastic Molding Electrical?
Plastic molding electrical refers to the manufacturing process where plastic materials are shaped into various components used in electrical devices. This process involves melting plastic pellets and injecting them into molds to create intricate shapes that are essential for circuit boards, connectors, and various electrical housing units. The versatility of plastic molding allows for complex designs that can be produced at scale, offering manufacturers both flexibility and efficiency.
Types of Plastic Molding Processes
There are several types of plastic molding processes that are prominent in electrical applications:
- Injection Molding: This is the most common type, where molten plastic is injected into a mold to create precise components. It is ideal for high-volume production.
- Blow Molding: Used for creating hollow objects, such as bottles or containers. This method is useful for specific electrical housings.
- Compression Molding: In this process, materials are compressed into a mold. While less common in electrical applications, it is used for certain larger components.
- Thermoforming: Here, plastic sheets are heated and formed over molds. This process is often used for packaging electrical devices.
The Benefits of Plastic Molding in Electrical Applications
Incorporating plastic molding electrical processes into manufacturing offers a multitude of advantages:
- Cost Efficiency: The ability to produce components at scale leads to significant cost savings in material and labor.
- Design Flexibility: Manufacturers are able to create complex shapes and intricate designs that would be difficult or impossible with traditional electrical components.
- Reduced Weight: Plastic components are considerably lighter than their metal counterparts, leading to lighter products that are easier to transport and install.
- Durability: Modern plastics can withstand impacts, chemicals, and extreme temperatures, making them ideal for various electrical applications.
- Insulation Properties: Plastic inherently provides electrical insulation, reducing the need for additional materials when crafting components for electrical systems.
Applications of Plastic Molding Electrical
The applications of plastic molding electrical are vast and continually expanding. Here are some common uses:
Consumer Electronics
From smartphones to household appliances, the consumer electronics industry utilizes plastic molded components extensively. Key parts include:
- Connectors and sockets
- Enclosures for circuit boards
- Keypads and buttons
Automotive Industry
In automotive manufacturing, plastic molding electrical is crucial for producing lightweight electronic parts such as:
- Control panels
- Wire connectors
- Sensor housings
Medical Devices
The medical device sector has specific needs for reliability and compliance with medical standards. Here, plastic molded components are found in:
- Monitoring equipment
- Diagnostic devices
- Wearable health tech
Industrial Equipment
Industrial applications also benefit from plastic molding electrical, particularly in the production of:
- Safety switches
- Instrument housings
- Control panels for machinery
Challenges in Plastic Molding Electrical
Despite the many advantages, there are challenges associated with plastic molding in electrical applications, which include:
- Material Selection: Choosing the right plastic for electrical applications can be complex, considering factors such as thermal stability and electrical conductivity.
- Mold Design: Creating molds that allow for precise detail can be costly and time-consuming.
- Quality Control: Maintaining consistent quality during the mass production of plastic components is crucial to avoid failures in electrical systems.
The Future of Plastic Molding in Electrical Applications
The future of plastic molding electrical is promising, with advancements in technology leading to even greater efficiency and effectiveness. Key trends to watch include:
- 3D Printing and Additive Manufacturing: These technologies are revolutionizing how molds are created, allowing for rapid prototyping and reduced lead times.
- Biodegradable Plastics: As sustainability becomes a priority, the development of eco-friendly materials will impact how electrical components are made.
- Smart Materials: The incorporation of intelligent plastics that can respond to environmental changes will lead to innovative electronic solutions.
Conclusion
In summary, the role of plastic molding electrical in the metal fabrication industry cannot be underestimated. With numerous benefits ranging from cost efficiency to design flexibility, it is no wonder that manufacturers are increasingly investing in this technology. As advancements continue to shape the future of manufacturing, businesses like Deep Mould are positioned to lead in creating innovative electrical solutions that address the challenges of modern production.
For companies looking to enhance their manufacturing processes or explore the potential of plastic molded components, engaging with experts in the field can lead to breakthroughs that elevate product offerings in a competitive market.