Understanding Titanium Rivets: The Future of Fastening Solutions
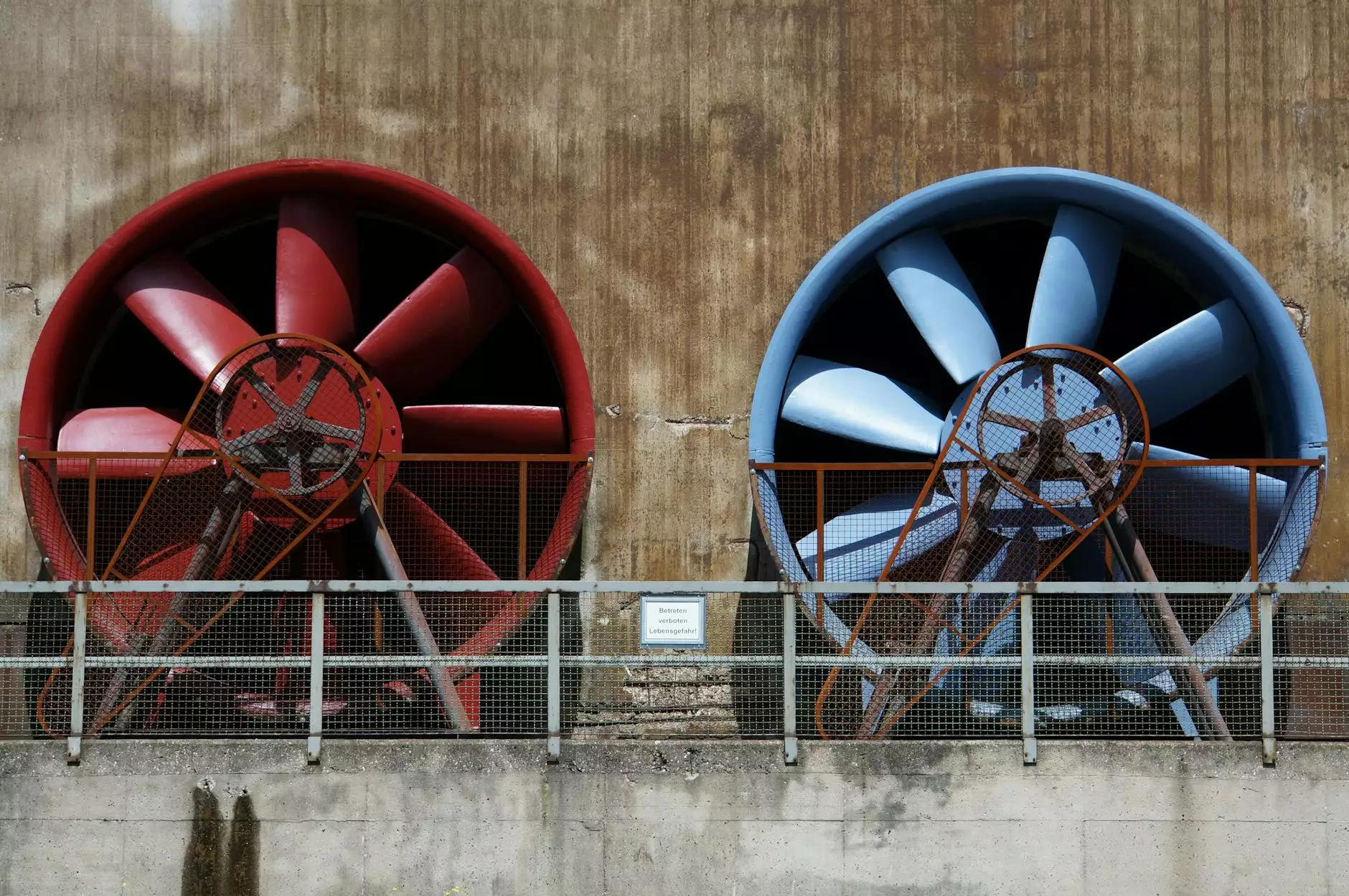
Titanium rivets are becoming increasingly essential in various industries due to their unparalleled strength, lightweight nature, and impressive corrosion resistance. This article provides an in-depth look at titanium rivets, their manufacturing processes, applications, and why they are the go-to choice for engineers and manufacturers worldwide.
What are Titanium Rivets?
Titanium rivets are fasteners made from titanium, a metal known for its high tensile strength-to-weight ratio and resistance to corrosion. These rivets are used to join materials together, providing a secure and durable connection. The use of titanium, especially in rivet manufacturing, enhances the fastener's performance in harsh environments, making them ideal for applications where traditional materials may fail.
The Manufacturing Process of Titanium Rivets
The process of manufacturing titanium rivets involves several critical steps:
- Material Selection: High-quality titanium alloys, such as Ti-6Al-4V, are commonly used due to their optimal balance of strength, weight, and corrosion resistance.
- Forming: The titanium ingots are heated and then shaped into rivets using advanced forming techniques, including forging or machining.
- Surface Treatment: To enhance their durability and resistance to the environment, titanium rivets are often subjected to surface treatments, such as anodizing or passivation.
- Quality Control: Rigorous testing ensures that each rivet meets the industry standards for performance and reliability.
Advantages of Using Titanium Rivets
The adoption of titanium rivets offers numerous advantages, making them an appealing choice for various industries:
- Lightweight: Titanium is significantly lighter than steel, which is crucial in industries such as aerospace where weight reduction can lead to fuel savings and increased efficiency.
- Corrosion Resistance: Titanium does not rust or corrode, making it suitable for marine applications and environments with high levels of moisture or chemicals.
- High Strength: Titanium rivets possess a high strength-to-weight ratio, providing strong joints even in demanding conditions.
- Biocompatibility: Due to their non-reactive nature, titanium rivets are suitable for medical applications, including implants and surgical instruments.
- Longevity: The durability of titanium results in longer life spans for applications, reducing maintenance and replacement costs.
Applications of Titanium Rivets
Titanium rivets find utility in a broad spectrum of industries:
Aerospace Industry
The aerospace sector demands lightweight yet robust materials to ensure the safety and efficiency of aircraft. Titanium rivets are extensively used in airframe assemblies and components, offering the strength needed to withstand extreme conditions.
Automotive Industry
In the automotive realm, manufacturers utilize titanium rivets to reduce vehicle weight without sacrificing safety or performance. High-performance vehicles, in particular, benefit from titanium due to its strength and lightweight properties.
Marine Applications
Because of their resistance to saltwater corrosion, titanium rivets are ideal for marine applications. From boat hulls to underwater structures, titanium ensures durability and longevity.
Medical Field
In the medical industry, titanium rivets are essential in surgical instruments and implants due to their biocompatibility. They reduce the risk of rejection and complications in patients receiving titanium-based implants.
Choosing the Right Titanium Rivets
Selecting the correct titanium rivets for specific applications involves several considerations:
- Size: The diameter and length of the rivet must be suitable for the materials they will join.
- Alloy Type: Different titanium alloys may offer variations in strength, ductility, and corrosion resistance.
- Coating: For additional protection, consider rivets with coatings for specific environmental conditions.
- Load Requirements: Understand the loads and stresses the rivets will experience in service.
Installation Techniques for Titanium Rivets
The installation of titanium rivets can be performed through several methods, including:
- Solid Riveting: Involves deformation of the rivet during installation to create a permanent joint.
- Blind Riveting: Suitable for applications where access is limited, allowing for the attachment of rivets from one side.
- Self-Piercing Riveting: This technique does not require pre-drilled holes, making installation quicker and reducing material damage.
Maintenance of Titanium Rivets
Although titanium rivets are low-maintenance, it is essential to monitor them periodically:
- Visual Inspections: Regularly check for signs of wear or damage.
- Corrosion Checks: Although titanium is corrosion-resistant, it is still advisable to inspect fasteners in harsh environments.
- Tightness Testing: Ensure that rivets remain securely fastened to avoid joint failure.
The Future of Titanium Rivets
The demand for titanium rivets is expected to grow in the coming years as industries look for innovative solutions that enhance performance while reducing weight and maintenance. Emerging technologies, such as additive manufacturing, could further revolutionize how rivets are produced, making them even more efficient and tailored to specific applications.
Conclusion
In conclusion, titanium rivets are an exemplary solution for a wide range of applications due to their unique properties and advantages. Whether in aerospace, automotive, marine, or medical fields, they provide a reliable and durable fastening solution. As technology progresses, the future of titanium rivets looks bright, promising even greater advancements in strength, performance, and application versatility. For those seeking high-quality titanium rivets, visiting titaniumbolts.com ensures access to top-notch products tailored to fit various needs. Embrace the revolutionizing strength of titanium in your next project!