Transform Your Business with Rapid Prototype Injection Moulding
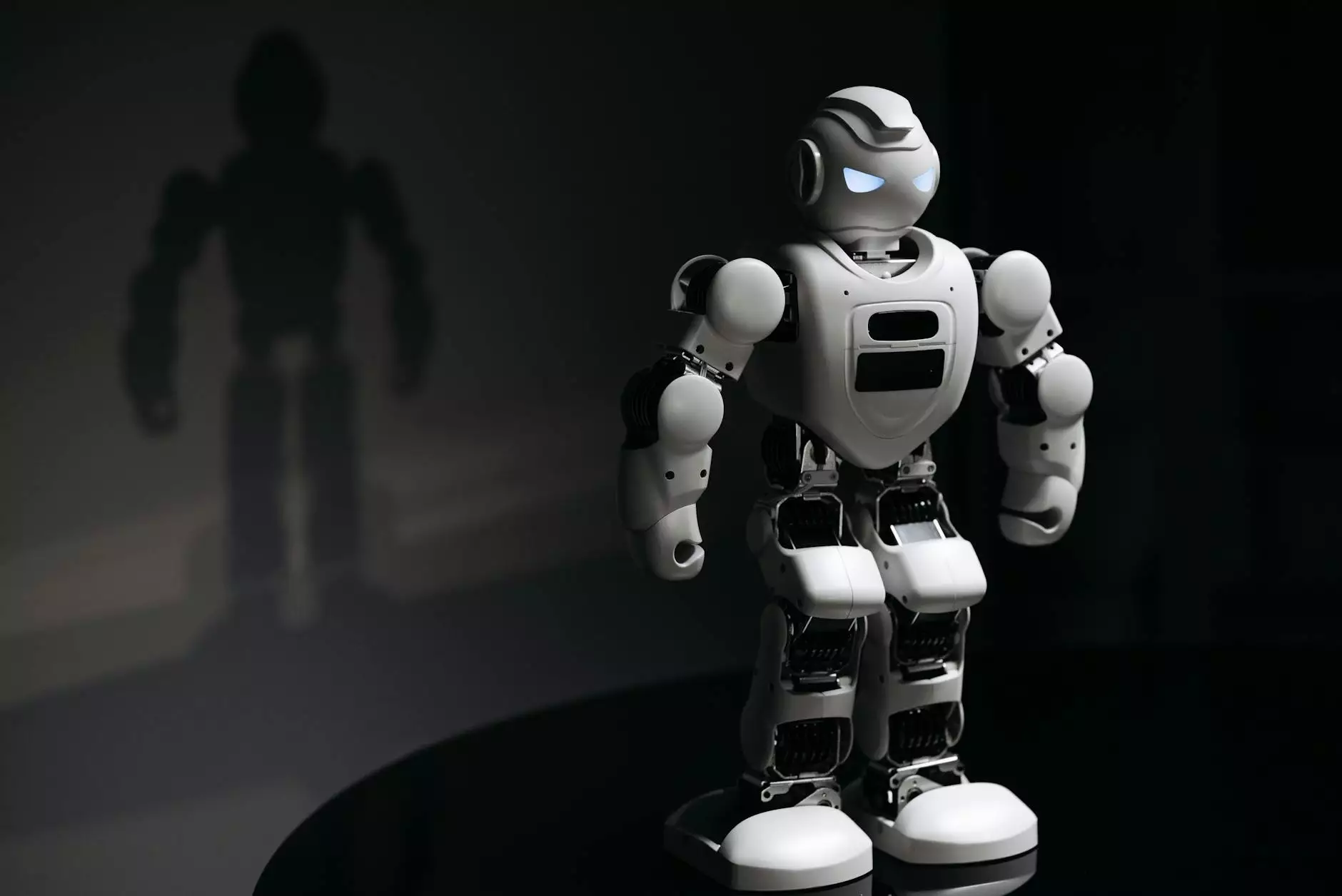
Rapid prototype injection moulding is revolutionizing the manufacturing landscape, providing a cutting-edge solution for businesses aiming to innovate and stay ahead of the competition. This advanced technique not only accelerates the development of prototypes but also enhances overall production efficiency. In this comprehensive article, we will delve into the myriad benefits of rapid prototype injection moulding, its applications, and how your business can leverage this technology for remarkable success.
Understanding Rapid Prototype Injection Moulding
At its core, rapid prototype injection moulding involves the quick creation of injection-moulded prototypes from 3D CAD models. The process allows businesses to produce physical parts quickly, cutting down lead times that traditional moulding methods require. This approach is particularly valuable during the product development phase, where companies can iterate designs based on feedback and insights swiftly.
The Advantages of Rapid Prototype Injection Moulding
Utilizing rapid prototype injection moulding offers numerous advantages that can drive your business forward:
- Speed: This method significantly reduces the time from concept to market, enabling businesses to respond quickly to market demands.
- Cost-effectiveness: By minimizing waste and streamlining production, companies can achieve substantial cost savings.
- Improved Design Flexibility: Rapid prototyping allows for easy modifications based on user feedback, ensuring the final product meets consumer expectations.
- High Precision: Injection moulding provides high dimensional accuracy, facilitating the production of intricate designs.
- Material Variety: A range of materials can be used in rapid prototype injection moulding, from plastics to metals, offering flexibility for different applications.
Applications of Rapid Prototype Injection Moulding
The applications of rapid prototype injection moulding span across various industries, highlighting its versatility and effectiveness:
- Automotive Industry: Used for creating components and interior parts, allowing for rapid testing and implementation.
- Consumer Electronics: Ideal for developing casings and intricate parts that require precision, contributing to faster product releases.
- Medical Devices: Enables the swift creation of prototypes for testing, ensuring compliance with regulatory standards while accelerating development cycles.
- Toys and Games: Facilitates the quick turnaround of designs to market, meeting consumer trends and demands.
- Industrial Equipment: Used for producing specialized components quickly, aiding in the efficient execution of projects.
How Rapid Prototype Injection Moulding Works
Step 1: Designing the 3D Model
The process begins with the creation of a 3D CAD model that outlines the design specifications of the component. This model serves as the digital blueprint for the subsequent stages.
Step 2: Tooling Design
Next, a mould is designed and manufactured based on the specifications of the 3D model. The tooling is optimized for speed and efficiency, reducing production time.
Step 3: Injection Process
Once the mould is ready, the chosen material is heated until it is molten, then injected into the mould. This process can occur rapidly, allowing for multiple prototypes to be produced in a short timeframe.
Step 4: Cooling and Finishing
After injection, the material is allowed to cool and solidify. The final prototypes are then removed from the mould and undergo any necessary finishing processes.
The Impact of Rapid Prototype Injection Moulding on Business Innovation
Leveraging rapid prototype injection moulding can significantly impact a company’s ability to innovate. By reducing lead times and allowing for quick adjustments based on market feedback, businesses can foster a culture of agility and responsiveness. This enhanced capability can lead to:
- Increased Product Quality: Iterative testing and rapid adjustments lead to improved designs and higher-quality final products.
- Faster Time-to-Market: The ability to develop and refine prototypes swiftly means products can reach consumers faster.
- Enhanced Collaboration: The rapid feedback cycle encourages collaboration between designers, engineers, and production teams, leading to a cohesive development process.
- Market Adaptability: Companies can quickly pivot in response to consumer trends, keeping them ahead of their competitors.
Addressing Common Misconceptions
Despite the benefits, there are misconceptions surrounding rapid prototype injection moulding that may hinder its adoption in some businesses. Here are a few common myths:
Myth 1: It’s Only for Large Companies
Many believe that only large enterprises can afford rapid prototyping, but advances in technology have made it accessible to businesses of all sizes. Small and medium-sized enterprises can also leverage this technology to enhance their product development processes.
Myth 2: It’s Not Suitable for Mass Production
While rapid prototyping is excellent for small batches and testing, it can also be scaled for mass production using the same moulds, making it a versatile option for various production needs.
Myth 3: It Compromises Quality
Some assume that rapid prototyping means compromising on quality. However, with high-precision moulding techniques, businesses can achieve exceptional quality standards, ensuring that prototypes and final products meet rigorous requirements.
Selecting the Right Partner for Rapid Prototype Injection Moulding
Choosing the right partner for your rapid prototype injection moulding needs is crucial. Here are some tips to consider:
- Experience and Expertise: Look for a company with a proven track record in rapid prototyping, particularly within your industry.
- Quality Assurance: Ensure that the partner has robust quality control measures in place to maintain high standards throughout the production process.
- Technological Capabilities: Assess the technologies the partner utilizes, ensuring they are equipped to deliver cutting-edge solutions tailored to your needs.
- Customer Support: Opt for a partner that offers excellent customer service and support throughout the project lifecycle.
Case Studies: Success Stories with Rapid Prototype Injection Moulding
Case Study 1: Automotive Component Manufacturer
An automotive component manufacturer integrated rapid prototype injection moulding into their workflow, enabling them to produce and test new designs faster than ever. The result was a 40% reduction in time-to-market for their new line of products, leading to increased sales and market share.
Case Study 2: Consumer Electronics Firm
A consumer electronics firm leveraged rapid prototyping to refine their product design based on early user testing feedback. By rapidly iterating their designs, they were able to enhance user satisfaction and secure a competitive edge in a crowded market.
Conclusion: The Future of Business with Rapid Prototype Injection Moulding
The adoption of rapid prototype injection moulding is not just a trend, but a transformative shift in how businesses approach product development and manufacturing. By embracing this innovative technique, companies can elevate their product offerings, streamline processes, and respond to market needs dynamically. As you look to the future, consider how integrating rapid prototype injection moulding into your operations can catalyze growth and innovation, positioning your business for greater success.
For more information on how rapid prototype injection moulding can enhance your business operations, visit deepmould.net today.