The Advantages of Industrial Laser Welders for Metal Fabricators
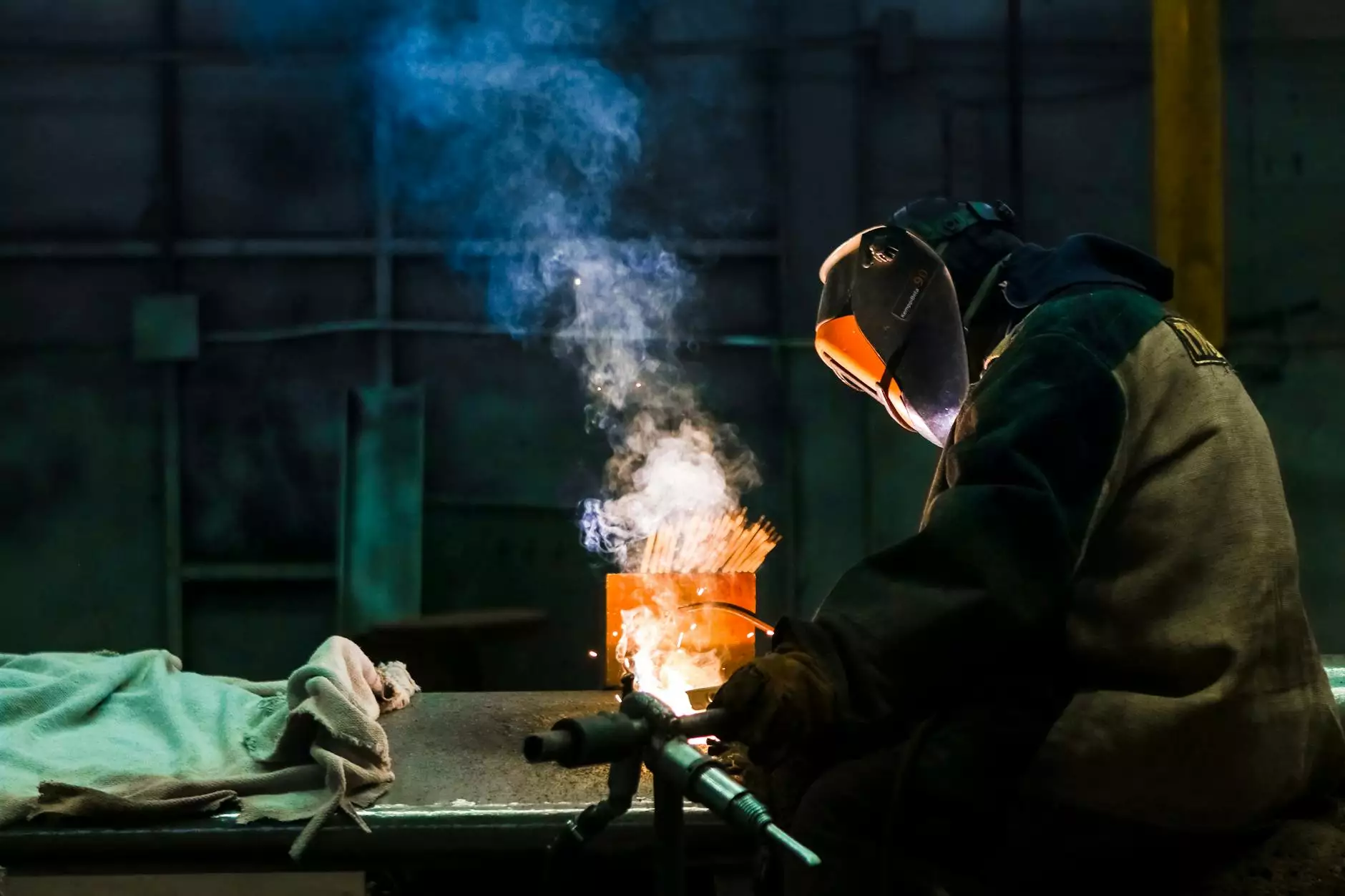
In the world of metal fabrication, precision and efficiency are paramount. This is where industrial laser welders shine. These advanced machines harness the power of laser technology to join metals with unprecedented accuracy and speed, making them an indispensable tool for modern metal fabricators.
Enhanced Precision
One of the key advantages of using an industrial laser welder is the unmatched precision it offers. Unlike traditional welding methods that rely on heat from an open flame or electric arc, laser welding focuses a concentrated beam of light on the exact point where the materials need to be joined. This pinpoint accuracy ensures that welds are consistently strong and clean, resulting in high-quality finished products.
Increased Efficiency
Efficiency is another hallmark of industrial laser welders. The speed at which these machines can create welds far surpasses that of traditional methods. With laser welding, fabricators can complete jobs in a fraction of the time it would take using conventional techniques. This not only speeds up production but also reduces overall costs, making laser welding a cost-effective solution for metal fabricators.
Wide Range of Applications
Industrial laser welders are versatile tools that can be used across a wide range of applications in metal fabrication. Whether you're working with thin sheets of metal or thick structural components, laser welding can provide precise and reliable welds on a variety of materials. This flexibility makes laser welders a valuable asset for metal fabricators looking to expand their capabilities and take on diverse projects.
Improved Quality Control
Quality control is a top priority for metal fabricators, and industrial laser welders can help ensure that every weld meets the highest standards. The precise nature of laser welding means that fabricators can achieve consistent results with minimal defects or imperfections. This level of quality control not only enhances the overall integrity of the finished product but also minimizes the need for rework or repairs, saving time and resources in the long run.
Environmental Benefits
Aside from their technical advantages, industrial laser welders also offer environmental benefits. Traditional welding methods often produce harmful fumes and waste, posing risks to both the environment and the health of workers. In contrast, laser welding is a clean and efficient process that generates minimal waste and emissions, making it a more sustainable choice for metal fabricators who are conscious of their environmental impact.
Cost-Effective Investment
While the initial cost of acquiring an industrial laser welder may seem daunting, it is important to consider the long-term benefits that these machines offer. With their enhanced precision, efficiency, and versatility, laser welders can streamline production processes, reduce operational costs, and improve overall quality. This makes them a worthwhile investment for metal fabricators looking to stay competitive in a rapidly evolving industry.
Conclusion
Industrial laser welders have revolutionized the metal fabrication industry with their unmatched precision, efficiency, and versatility. Metal fabricators who incorporate laser welding into their processes can expect higher quality results, faster production times, and reduced costs. By harnessing the power of laser technology, businesses can stay ahead of the curve and meet the evolving demands of the modern market.
Explore the opportunities that industrial laser welders can bring to your metal fabrication business. Contact dplaser.com today to learn more about our cutting-edge welding solutions tailored for metal fabricators.